Vibration surveys are carried out for a variety of reasons over the lifetime of a facility for semiconductor fabrication (fab) or other advanced technology process.[1] Evaluations may take place as part of the site selection effort, during construction, or during the productive life of the facility. Generally, there should be a reason for a vibration survey—a question or set of questions that need to be answered. That reason will likely suggest an appropriate time at which a survey should be carried out. However, it is not unusual for a survey to be scheduled at an inappropriate time, which may lead to useless data, or data that lead to an incorrect conclusion.
The question or questions providing the reason for the survey may not even be answered. For example, suppose the object of the survey is to assess whether the vibration design goals of a facility have been met. In essence, the survey is intended to predict the quality of the vibration environment in a fab after it becomes operational. When operational, the vibration environment is some combination of ambient site vibrations, vibrations generated by the facility’s mechanical systems (fans and air handling systems, pumps and liquid circulation systems, etc.), and those generated by personnel activities. Will the survey objective be met by a site survey carried out during the construction phase, in the middle of the night (to avoid construction activities), prior to turning on the mechanical systems? Most likely not. Ambient site vibrations will likely be at their lowest during the night, and there will be no contribution from the ubiquitous mechanical systems.
The intent of this article is to identify some of the reasons for vibration surveys and discuss the appropriate timing for those surveys. This will necessarily involve some discussion of the IEST/ISO operational states of a fab as well as some aspect of measurement protocols. The issue of facility “maturation” will be touched upon, but a detailed presentation of that phenomenon is beyond our present scope. Measured data from multiple surveys taken over periods of many months (or several years) will be used to illustrate the discussions.
PURPOSES OF FACILITY VIBRATION SURVEYS
It is quite common to carry out a vibration survey of a site prior to construction of a facility. This may be just the first of several vibration evaluations carried out over the life of a fab. There are a variety of reasons for these subsequent surveys, some of which are discussed below.
Site Survey — The purpose of the pre-construction site survey is to aid in the site selection or acceptance effort. There is a limit to the amount of attenuation of poor site vibration conditions that can be achieved at or inside a building. Thus, depending on the circumstances, it may be necessary to verify that vibration due to external sources (rail and automobile traffic, industrial facilities, etc.) will be adequately low for the proposed function of the site and future buildings and processes.
Fab Construction Process — At least two occasions during the construction phase provide opportunities to evaluate distinct characteristics of the facility with a minimum of interference from extraneous conditions. Surveys done at these two times would serve quite different purposes. Those surveys are the primary focus of this paper. The earlier of the two is what we often call a “Structural Evaluation;” the later one we commonly call a “Final Evaluation” or “As Built Evaluation.” Both may be somewhat extensive in scope.
Tool Site Evaluation — This type of evaluation is generally rather limited in scope. Its intent is to evaluate the planned locations for one or more particular tools to document that those locations meet the tools’ specific installation requirements.
Diagnostics — As a fab matures, problems may occur with ageing mechanical systems or specific tools, which may suggest that vibrations are exceeding a particular tool’s tolerances. The vibration measurements are more of a diagnostic aid for the vibration consultant as a source of excessive vibration is sought.
Documentation of “Current” State — Some facility owners wish to update their records periodically with regard to the environmental status of a production area as a facility ages. This may include vibration and/or acoustics surveys as well as particulate surveys.
The timing of the last three survey types is somewhat obvious. Circumstances or owner policy will dictate when they must be carried out. The timing of the surveys carried out during construction is less obvious, and poor timing can lead to misleading results, or complications with remediation of any inadequacies they identify.
The intent of a structural evaluation is to validate specific structural parameters associated with the structural dynamics design, such as the stiffness and resonance frequencies of floors, performance of structural isolation breaks (SIBs), and structural attenuation or amplification between points in the fab (such as between the subfab and fab). If inadequacies[2] are found, they are much more easily corrected during construction than after the cleanroom and mechanical systems are in place and operating.
The intent of a final evaluation is to document the performance of the vibration-critical portions of a fab at the time that the facility is “delivered” to the owner. Inadequacies may be found at this time as well, but those inadequacies are (hopefully) limited to easily correctible items such as improperly aligned vibration isolators for mechanical systems.
VIBRATION CRITERIA
Vibration criteria fall into two categories—tool-specific and generic—and their usage depends upon the nature of the evaluation. In general, a facility will include more than one tool, so we try to avoid designing a facility to meet the requirements of a specific tool. On the other hand, if a specific tool site is being evaluated—whether for installation validation or diagnostic purposes—the manufacturer’s criteria are most appropriate.
Designing a facility for a specific tool might severely limit the future flexibility of that facility.[3] In addition, different manufacturers state their criteria in different ways, which may lead to inconsistencies if they are used together. For example, one manufacturer may state their criterion in peak-to-peak displacement, while another might give theirs in rms velocity, and yet another in peak acceleration.
It was for these reasons that generic vibration criteria were developed. Two popular families of criteria are based on the group developed two decades ago by Ungar and Gordon (1983) while they were employed at Bolt Beranek and Newman (BBN). Slight modifications have occurred over the years, and they are now promulgated by IEST (1993, 2005), where they are denoted by the acronym “VC” (VC-A through VC-G), and ASHRAE (1999), where they are denoted by a “Class” designation (Classes A through F).[4] The VC curves are shown in Figure 1.[5] The issue of generic criteria (along with the related measurement methodologies) is explored at greater length in Amick (1997).
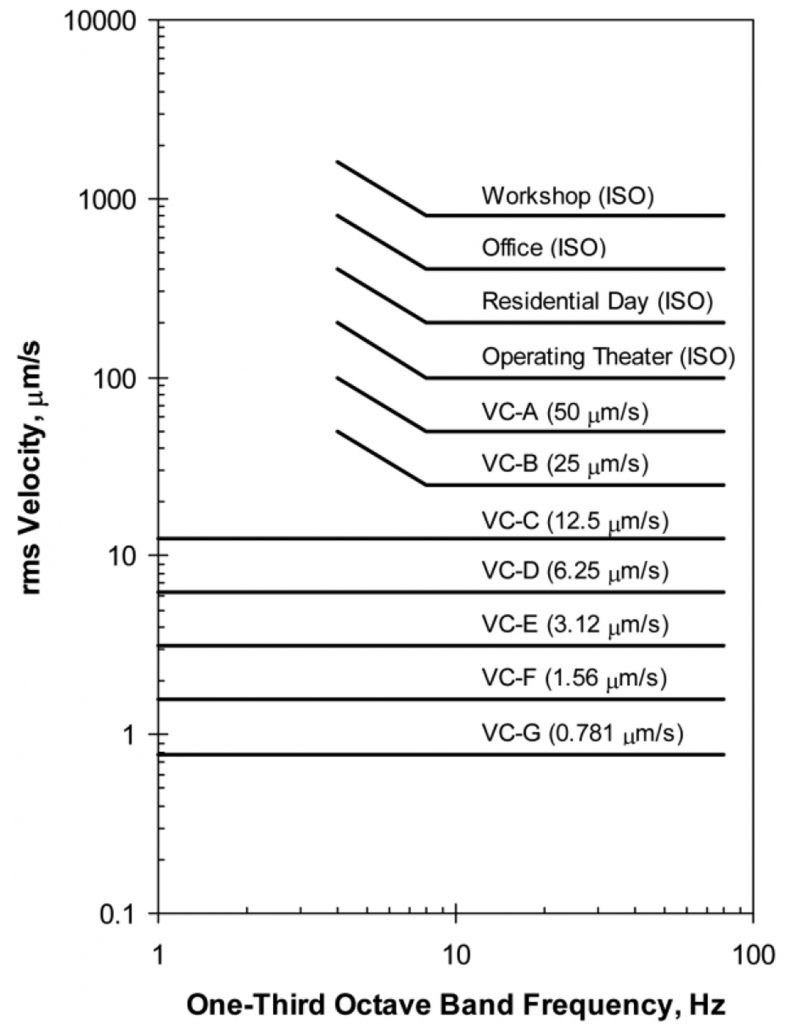
The generic vibration criteria are based in part on the environmental vibration specifications provided by tool manufacturers. The latter environments are expected by the manufacturer to be present at the time the tool is installed. It is appropriate to apply them to tool-specific measurements, which are generally made at any time in an operational fab. However, if the intent is to demonstrate that a fab as a whole conforms to its design goals, the survey and the criteria should represent as much as possible the total environment encompassed by the design (and thus the responsibility of the design team). Ideally, the survey should be made with all of the mechanical systems provided by the design and construction teams in an operational state, before systems are installed which are not the responsibility of the design and construction teams. The appropriate criterion is that used for the design of the facility is presumably a generic criterion.
MEASUREMENT STATISTICS
Measured vibration data are commonly acquired as analog time history signals produced by acceleration or velocity transducers such as accelerometers or seismometers, respectively. From a data analysis viewpoint, Amick (1997) divided time history signals into two broad categories, after Bendat and Piersol (1986), each with two subcategories, as follows:
- Deterministic data signals: (a) steady-state signals; (b) transient signals.
- Random data signals: (a) stationary signals; (b) nonstationary signals.
Ambient site vibrations are usually a mix of steady-state (sinusoidal, generally from mechanical equipment) and stationary (random, from a variety of sources). Thus, a site or building vibration survey involves measurement protocols appropriate for these environments, generally involving energy-average signal processing. However, there are often transient vibrations, such as those associated with vehicle pass-by, and these may require the use of maximum-hold processing or centile analysis [Amick and Bui (1991)].
Temporal Statistics — It is customary to characterize the vibration environment at some location by means of the energy average (linear average) spectrum, or a centile spectrum approximating the linear average, such as L10.[6] If one is documenting a transient event, such as a truck or train pass-by, it may be more appropriate to use a spectrum form that captures or approximates the upper bound of the spectrum occurring during the event, such as the maximum-hold spectrum (often denoted Lmax). In some cases with centile processing, the L1 spectrum will be used, so as to eliminate the effect of extremely short-duration transients which may not be truly representative of the event.
If the vibrations at a measurement location are stationary (or a reasonable approximation of stationary), then a relatively short sample time (e.g., 1 to 2 min) is acceptable to capture the linear average, but a longer sample time (e.g., 10 to 30 min) may be desirable if centile processing is being used. If Lmax is being obtained using either maximum-hold or centile processing, it is important to note that Lmax increases as longer sample times are used, even if the environment is stationary.
Spatial Statistics — If one is characterizing a single location, such as that of a proposed tool, then it is logical to use a single measurement location, though some will measure several points around the footprint of the tool. However, if one is attempting to characterize a large area, such as an entire cleanroom, a single location is probably not representative of the whole. One can either present all of the measured spectra, or use some format in which all the spectra are condensed into a single spectrum or set of spectra.
A practice has evolved in which the ambient vibrations of a fab or other large area are characterized by a spectrum representing the mean plus one standard deviation spectrum, Lmean+sig, of a collection of spectra obtained at a statistically significant number of locations randomly distributed throughout the cleanroom or other area of interest. The Lmean and Lsig spectra are defined for a collection of spectra Xi as
log (Lmean)=Average(log(Xi))
(1)
log(Lsig)=StdDev(log(Xi))
(2)
The statistics are calculated for each frequency. The two spectra are combined in log space to obtain Lmean+sig, defined as[7]
log (Lmean+sig)=log(Lmean)+log(Lsig)
(3)
When presenting data in a report, we will typically summarize the data in a plot that shows four spectra: Lmin, Lmean, Lmean+sig, and Lmax. The Lmean+sig spectrum is usually shown in a bolder line. The reader can then easily see the range of the data, the statistically meaningful representations, and the spectrum used to characterize the space as a whole, Lmean+sig. If one wants to compare the performance of the entire space at two different times, one may show the Lmean+sig spectra from each set of measurements.
OPERATIONAL STATES OF A FAB
Vibrations may come from a number of sources. Some may be from distant activities such as vehicle or rail traffic, or even from minor seismic activities. No matter how remote, we will find these vibrations, and they may be called “cultural” vibrations. As a site transitions from remote to developed, the level of vibrations generally increases. The presence of a building will alter the vibrations in a number of ways, including the contributions from its mechanical systems. It is important to carefully consider the point in time at which a survey is made, and the nature of the associated cultural vibrations.
Several key milestones in the life of a facility may be defined. It may be appropriate to carry out measurement programs at each one for one reason or another, but there might be important reasons why specific benchmark measurements should be done at particular milestones. These milestones may be defined in terms of pre-construction, during construction, and post-construction. We find industry standardization of some of the milestones, but not of others. The process of commissioning or certification forms a boundary of sorts between construction and post-construction. We will consider it part of the former, as one of its purposes is to document the performance of the deliverable—the completed facility.
Pre-Construction Milestones — We make a distinction between two site states. We use the term “greenfield” to denote a site at which there are no existing facilities, and “developed” to denote the site of a future building on a large piece of property with one or more existing facilities (e.g., a “campus”). The distinction is between whether there are other operating facilities at the time of the survey. Thus, when considering a campus (or industrial park) that will have multiple fabs, the very first set of measurements could be considered “greenfield” and measurements subsequent to startup of the first fab would be considered “developed.”[8]
Construction Milestones — The most important vibration evaluation during construction is the one that takes place as the completed facility is “delivered” to the owner. We call it the “final” evaluation. It demonstrates that the facility performs as intended, at the time the owner takes possession.
The “final” evaluation is intended to document the “as built” state, as conventionally accepted. ISO Standard 14644 defines this state as “all construction is complete, all services connected and functioning but with no production equipment, materials or personnel present.” In this state, tools have not yet been installed, but equipment associated with the facility itself (i.e., fans, pumps, chillers, etc.) are running normally and there is flow in the ducting and piping. It should be acknowledged that this is an idealized condition, and very rarely occurs, since most owners start installing production equipment before the facility is fully certified. Also, it is not possible to run all electrical and mechanical equipment at normal operating conditions at this time, as the tools are not in place to provide a “load”. However, a reasonably good approximation of this state can usually be (and indeed must be) achieved.[9]
Post-Construction Measurements — There are several reasons to carry out a vibration survey at some time after the “as built” state not longer exists. ISO Standard 14644 defines two states in which measurements of various sorts are commonly carried out in a fully functional facility: “at rest” and “operational.” The “at rest” state is defined as one in which tool “installation is complete with equipment installed and operating in a manner agreed upon by the customer and supplier, but with no personnel present.” The “operational” state is one in which the “installation is functioning in the specified manner, with the specified number of personnel present and working in the manner agreed upon.” These two states are also quite idealized, and the only significant differences between the two are the presence of personnel and the state of productivity. There may be a significant difference in the particle count or acoustic noise in these two states, but the only significant manner in which vibrations are affected are with regard to walker-generated vibrations and material handling (such as automatic vehicles or other rolling loads).
It is not uncommon to find a significant difference in the vibration environments in the “as built” and the “at rest” or “operational” states. We have observed a variation that can occur over time as a facility ages. New tools are installed, or old ones modified, and often this will add to the vibration environment. We call this effect “maturation” and use the term “mature” to describe an older facility in which the vibration environment has evolved.
FAB MATURATION PROCESS
A detailed discussion of the fab maturation process is beyond the scope of this paper, but a condensed discussion is appropriate. A lengthy discussion was presented by Gendreau and Amick (2004). Several factors contribute to the vibration environment in a fab or other completed technology building:
- Greenfield Site ambient vibrations — These are due to such varied sources as distant traffic or other transportation sources, small microseismic events, etc., and exist at the site with or without the presence of the building [Gordon (1987)]. These are sometimes called “cultural” vibrations.
- Developed Site ambient vibrations — These are due to the added presence of other buildings on the site (including their mechanical systems), as well as the added cultural vibrations associated with on-site traffic, etc.
- “Building Effect” — This results from a soil-structure interaction, whereby the presence of the building’s mass and stiffness suppresses some vibration components and may amplify others. A detailed discussion of this effect is beyond the scope of this paper, but is addressed by Amick, et al. (2004).
- Building mechanical systems — Vibrations are generated by the mechanical systems that are required in any technical building, including pumps, air handling systems, air flow, fluid flow in piping, etc. Most of these factors are controlled to some extent using vibration isolation methods, but the effects are only reduced, not eliminated. In addition, the effects may be reduced only temporarily if the isolation methods and devices are not properly maintained.
- Owner-installed mechanical systems — Many items of mechanical equipment, particularly vacuum pumps, must be installed with production or research equipment. Typically, these are installed after the building has had its “as built” evaluation, and are the responsibility of the owner/operator, rather than the design/construction team.
- Building occupants and personnel activities — Personnel must walk about the building. Material must be moved. Goods must be delivered. All of these activities generate vibrations. The effects of these sources may be addressed to some extent, but they are only reduced, not eliminated.
It should be clear that when one considers all these factors and now they may change over time, a facility vibration environment cannot be static over any extended period of time, especially as a facility progresses from greenfield site to operational facility. In fact, developed site ambient vibrations and those from owner-installed mechanical generally increase over time as an area is built up and new equipment is installed. This is the primary part of the process we call maturation.
Maturation of one facility is illustrated in Figure 2, which shows two constant-bandwidth spectra, each of which is the Lmean+sig resulting from measurements at 22 locations in a representative semiconductor production cleanroom. The same 22 locations were used in both surveys, but the surveys were significantly separated in time. The first was a formal[10] “as built” survey, and the second was an “at rest” survey taken 20 months later.
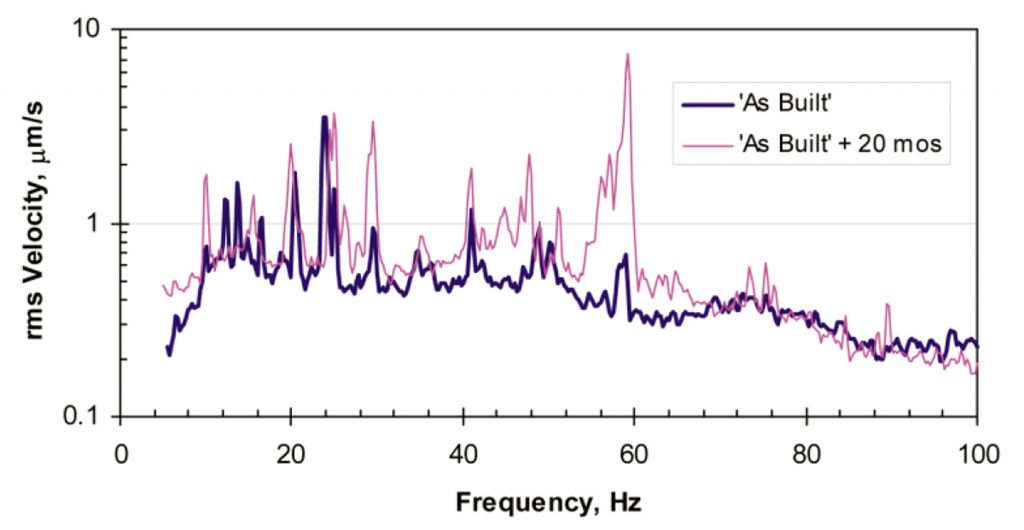
The sharp peaks in Figure 2 correspond to vibrations generated by rotating mechanical equipment operating at single frequencies. Broader peaks—though still sharp—are formed when a number of single-frequency peaks are at nearby frequencies. We see considerable increases at frequencies between 55 and 60 Hz, and between 28 and 30 Hz. Other minor increases occur at other discrete frequencies, as well.
The increases are shown more clearly in Figure 3, which presents the change in terms of the ratio of the “at rest” spectrum divided by the “as built” spectrum. The shaded area represents changes of 6 decibels (from halving to doubling). Though some of the increase may include performance degradation of isolators on building mechanical systems (which can occur over time), we have found that the vast majority of maturation-related increases are due to new equipment installed as part of production systems (such as dry pumps).
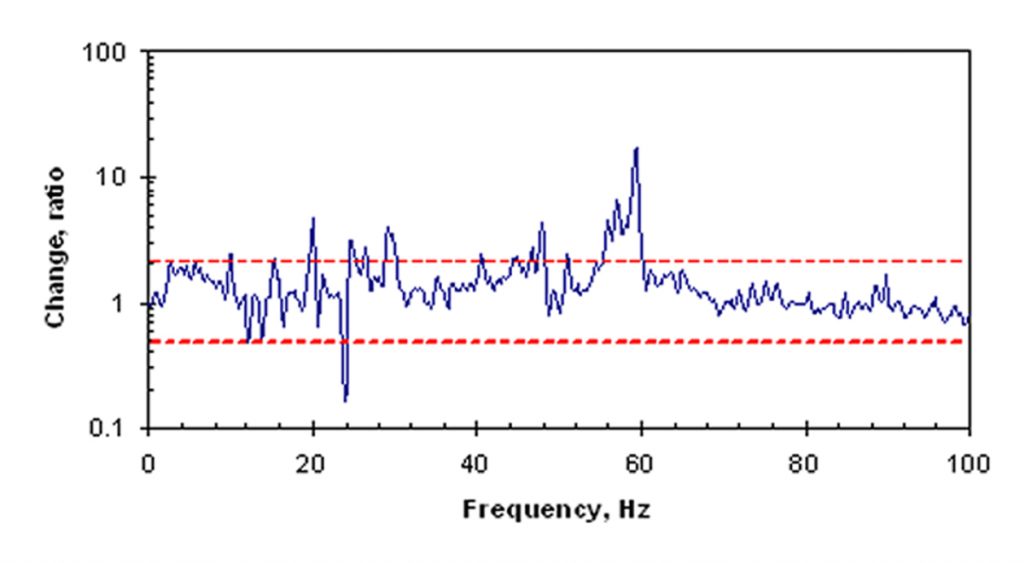
MEASUREMENTS FROM A REPRESENTATIVE FACILITY
We are in the process of gathering vibration data measured at several fabs over a long period of time. The data for one such facility are shown in Figure 4. This facility is one of several on a campus and was just about to go into production at the time of the most recent survey. In addition to the design criterion VC-D, the figures show data from four studies:
- The greenfield site survey, prior to any of the fabs on the campus being constructed. There was little development in the area nearby.
- The site survey for the fab under discussion. The survey was carried out prior to starting construction, but after several other nearby fabs on the campus had been in operation for some time. This was a “developed site” survey. Measurements were made at several locations within the footprint of the fab, and the spectrum shown is Lmean+sig.
- Ambient vibrations measured during the structural evaluation. Normally, the intent of this evaluation is the measurement of stiffnesses, resonance frequencies, and transmission properties of the facility, and all of these measurements benefit from being carried out at the quietest possible time. The structure itself was completed and some of the building shell was in place, but none of the mechanical equipment was operating. The measurements were made in the middle of the night, without any other construction activities.
- Ambient vibrations measured on the structural floor of the cleanroom at a number of randomly selected locations distributed throughout the cleanroom, represented as an Lmean+sig spectrum. These measurements were made in approximately the “as-built” state. The cleanroom and the mechanical infrastructure were fully operational and ready for certification. A few tools had been installed but were not operational, and there was minimal personnel activity. However, this is the “quietest” state achievable while maintaining clean class.
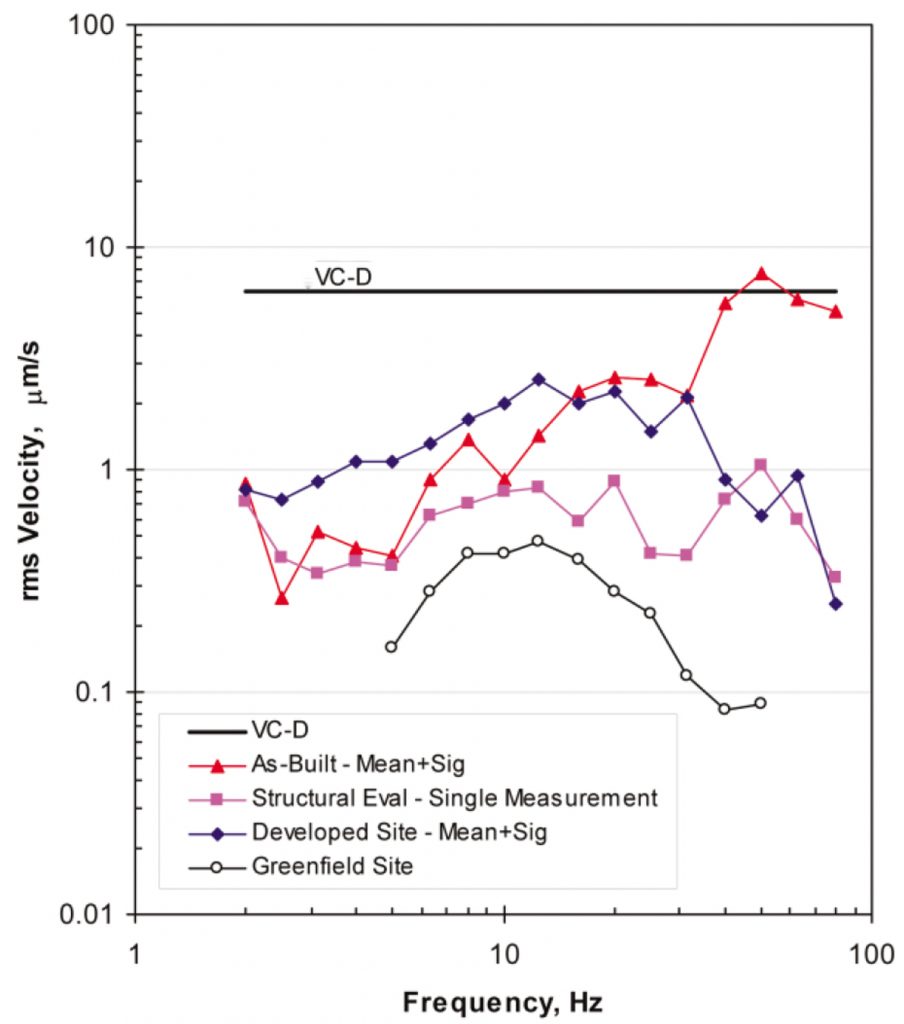
Table 1 summarizes the maxima from the four spectra. The predominant vibrations prior to construction are in the 12.5 Hz band, the predominant site frequency. After construction, the predominant vibrations are in the 50 Hz band, which contains the floor’s vertical fundamental resonance frequency.
Table 1. Summary of vibration maxima (in one-third octave bands) from four surveys at a fab and on the site prior to construction.
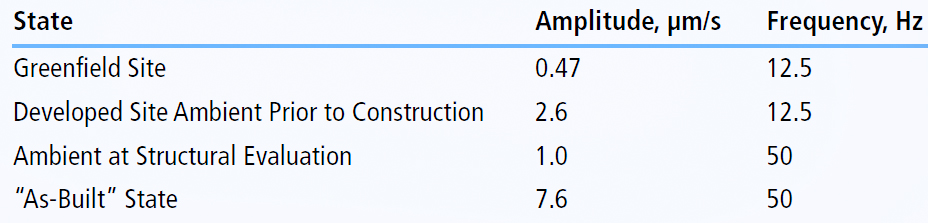
These data are shown in sequential order in Figure 5. Several things are important to note:
- The presence of other fabs on the campus introduce a significant amount of vibration energy to the site. There is an increase by a factor of 5.5 times (15 dB) associated with development at the campus. All of the fabs have had about the same level of effort given to vibration control.
- The fab building itself tends to suppress some of the vibration energy when there are no vibration sources within the building. We call this the “building effect.” In this case, there was a reduction by a factor or 0.4 (8 dB)[11].
- The increase from site ambient prior to construction to the as-built state is by a factor of 2.9, about 3 dB. There is a much greater difference from structural to as-built, 7.6 times (18 dB), due to operation of the well-isolated building mechanical equipment.
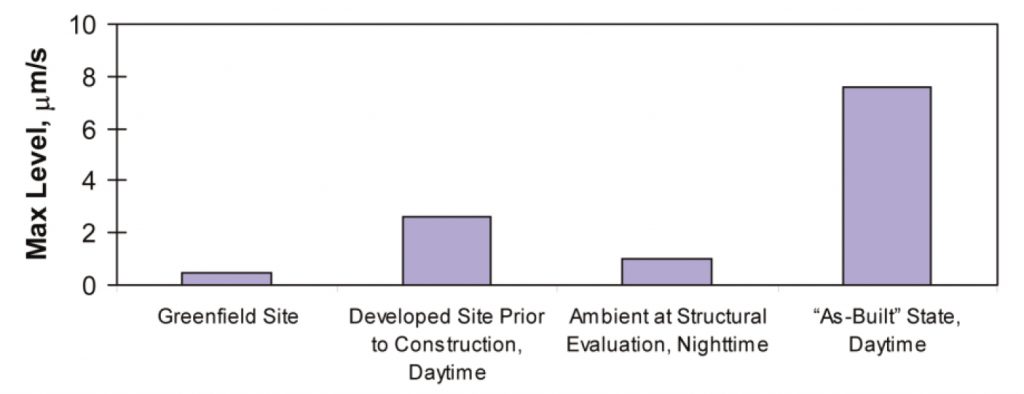
It is clear that data taken prior to the introduction and operation of mechanical equipment is not representative of the environment presented to fab tools when they are installed.
RECOMMENDATIONS
When considering the timing of a vibration survey, one should start by asking one important question: “Why do I want this survey?” The answer may dictate when you have your survey carried out. Following are some possible answers to the question, and the measurement times suggested for each. We have carried out surveys based upon all of these questions.
Do I want to buy this piece of property?
“Greenfield” conditions; during times at which the site is most energetic (rush hour traffic, fastest traffic, rail passages, etc.). If your facility will be used for research, your scientists may want to know how it performs in the middle of the night. This is relevant only if they can work during off hours.
Is this location on my campus acceptable “as is”, or do I need to take corrective action, perhaps with respect to a neighboring building or traffic layout?
“Developed site” conditions; during conditions when the most mechanical systems are running in existing facilities and environmental vibrations are at a maximum (rush hour traffic, fastest traffic, rail passages, etc.).
Does the structure meet its engineering design parameters, such as stiffness, resonance frequencies, propagation properties, etc.?
During construction phase, after main load-bearing structural elements are in place (foundation, columns, shear walls, floors, etc.) Formwork must have been removed, and concrete cured to design strength (at least 28 days). Measurements must be made without impact from construction and are often done at night. Ambient vibration may be documented to validate measurement quality, but these measurements do not predict the final vibration environment to which the tools will be subject.
What is the effect of this particular building foundation and structure at this site and with this construction type?
This is rarely needed, but if it is, it can be done any time after the foundation and a significant portion of the structure are complete. The test should be scheduled at a time that interior activities are at a minimum, and exterior activities may be controlled by the evaluation team.
Does the facility meet its performance goals? Is it ready to deliver to the owner?
Ideally, the “as built” state, meaning mechanical systems are operational but production or research equipment is not. Survey should be carried out during normal working hours, if possible. Avoid taking data during disruptive construction or tool installation activities.
A survey carried out prior to startup of the facility’s mechanical systems will not provide the documentation required by this question.
What is the current vibration environment of my facility?
Presumably, you want to document the normal working environment of your facility. Carry out the survey under either at rest or operational conditions, but document which one. The survey should be (1) at a time representative of normal working conditions, or (2) at the most energetic time of day (for “worst case” condition). A spatial statistical evaluation of multiple points might be the most useful, especially if comparing with similar data from the past.
What is the current vibration environment at a tool location?
Carry out the measurement under either at rest or operational conditions, but document which one. The measurement protocol should be consistent with the tool manufacturer’s requirements.
What is the quietest my facility can be?
This isn’t usually done for fabs, but is often of interest for research facilities, where scientists may wish to work at the “best” time. This survey may require several measurements to document the diurnal variation. A continuous 24-hr survey with centile processing may be useful. This is discussed in Amick and Bui (1993).
A survey carried out in the middle of the night during the construction phase will likely not give a correct answer, as it will not include the effects of mechanical equipment. If the mechanical systems will be operating at the quietest part of a normal day, they must be operating during the vibration survey. One may also wish to know the contribution due to equipment operable by the user, in case temporarily powering these off may provide an improvement in the vibration environment.
CONCLUSION
A vibration survey (or any environmental survey, for that matter) can be costly, and it should be money well spent. Most surveys have an objective—a question to be answered. The scheduling of the survey should be driven by what one wants to know. If the objective is to assess a site’s suitability, and it is to be used during the day, then evaluating it in the middle of the night will not characterize how it will perform during the day. If the facility is to be used at night, that is another matter. If it is to be used both day and night, it might be important to have data for both time periods.
Likewise, if you are characterizing your fab, schedule the survey so that its results characterize the operational state you really want characterized. An as-built survey cannot be carried out prior to the mechanical equipment being installed and balanced. An as-built survey will not necessarily represent how a facility will perform after a year of use (and modification). A survey when the facility is in full production probably will not document whether the design/build team met its contractual obligation to deliver to you a facility with particular vibration criteria.
All this sounds terribly obvious, but several times a year we are asked to evaluate a facility at the “wrong” time. In one typical case we were asked to measure vibrations for a 24-hr period during construction (after the structure was completed) and predict the vibrations in the cleanroom. Since the site was “contaminated” by construction during the day and very quiet at night, it was unreasonable to use any part of this survey to characterize the time when the cleanroom’s recirculation air handlers, ducting, and chilled water piping was operational. The money would not have been well spent.
One particularly troubling case—mentioned above—came to us as a diagnostic problem: “Why isn’t our brand new fab meeting tool specs?” The consultant used during design had carried out a midnight survey during the middle of the construction phase in order to characterize how the fab would perform during operation. The owner was lulled into a sense of security by the fact that at midnight at this semi-rural site, the midnight vibrations were an order of magnitude below the facility requirements. Nobody considered the effects of the mechanical systems. It turned out the design and construction both had some flaws, most of which could have been identified and mitigated if the survey had been delayed until the “as-built” stage and owner acceptance based upon the fab’s performance at that time. A significant amount of production was delayed by the need to correct the problems so the tool requirements could be met.
These minor catastrophes don’t have to happen to you. Use common sense to schedule surveys when they will provide the information you need. Be sure to communicate to your vibration consultant the reason why the survey is being done. Any experienced vibration analyst should be able to double-check your assumptions regarding timeliness, and help you get the information you need when you need it.
Footnotes
- This paper specifically addresses vibration surveys, but most of the issues we raise apply equally well to other environmental “contaminants,” including EMI, acoustic noise, particulates, and airborne molecular contaminants. ↑
- These inadequacies could include design flaws, construction defects, misinterpretation of design, etc. ↑
- Suppose a facility was designed for a particular stepper with moderate vibration requirements. A few years into operation, the owner may see the need to convert to a more current model or to a different technology, such as a scanner. The manufacturer’s criterion for the later tool might be more stringent than those of the earlier one. Generic criteria—though conservative—are intended to avoid this problem. ↑
- The reader is cautioned that the letter designations of ASHRAE (2003) are not the same as those used in IEST (1993, 2005). For example, the ASHRAE Class B criterion corresponds to IEST VC-D (both are 6.3 m/s). ↑
- The VC curves are being updated in the version to be issued in the 2005 edition of IEST RP-12. The newer version is shown in Figure 1. ↑
- When using centile spectra, the designation Ln denotes the spectrum that is exceeded n percent of the time. This is discussed at greater length in Amick and Bui (1991). ↑
- Carrying out statistical operations on levels expressed in decibels produces the same results as operations in log space. The latter is simply a more general format for definition. ↑
- The presence of commercial, industrial, or transportation facilities on adjacent property may contribute to the site vibration environment to some degree, but they are not considered as part of the distinction between “greenfield” and “developed”. It is important to note, however, that future significant changes in this “external” environment (i.e., the addition of a rail system) can have a significant impact on the future use of a site, and so these are also considered, to the degree possible, in a pre-construction site survey. ↑
- An important distinction must be made with regard to EMI surveys. EMI is highly dependent on load (i.e., electrical current), and a proper as-built EMI survey will require the use of artificial loads. ↑
- We are calling this a formal “as built” survey because the owner elected to start installing production equipment only after the “as built” documentation surveys were completed. Thus, we could be assured that there was no contribution from owner-supplied equipment. This formality is rarely followed now. ↑
- In some situations, there is a diurnal variation in vibrations. In many others, particularly at locations with around-the-clock production and constant load on mechanical systems, there may not be. The engineer must exercise some judgment as to whether this is relevant in a given study. ↑
REFERENCES
Amick, H. (1997). “On Generic Vibration Criteria for Advanced Technology Facilities: with a Tutorial on Vibration Data Representation,” J. Inst. Env. Sci., September/October 1997, v. XL, no. 5, pp. 35-44
Amick, H., and Bui, S. K. (1991). “A Review of Several Methods for Processing Vibration Data,” Proceedings of SPIE Conference on Vibration Control and Metrology 1619, pp. 253-264, San Jose, CA (November 1991)
Amick, H., Gendreau, M., and Bayat, A. (1999). “Dynamic Characteristics of Structures Extracted From In-situ Testing,” Proceedings of SPIE Conference on Opto-mechanical Engineering and Vibration Control, July 20, 1999, Denver, Colorado
Amick, H., Xu, T. and Gendreau, M. (2004). “The Role of Buildings and Slabs-on-Grade in the Suppression of Low-Amplitude Ambient Ground Vibrations,” Proc. 11th Intl. Conf. on Soil Dyn. & Earthquake Engng. (11th ICSDEE) & the 3rd Intl. Conf. on Earthquake Geotech. Engng. (3rd ICEGE), 7-9 January, 2004, Berkeley, CA.
ASHRAE (2003). ASHRAE Handbook: Applications, Chapter 46, “Sound and Vibration Control,” 47 pp.
Bendat, J. S., and Piersol, A. G. (1986). Random Data: Analysis and Measurement Procedures, 2nd ed., John Wiley & Sons, Inc. (1986).
Gendreau, M. and H. Amick, “’Maturation’ of the Vibration and Noise Environments in Semiconductor Production Facilities,” Proc. ESTECH 2004, 50th Annual Technical Meeting, Institute of Environmental Sciences and Technology (IEST), Las Vegas, Nevada, April 28, 2004
Gordon, C. G. (1987). “A Study of Low-Frequency Ground Vibration in Widely Differing Geographic Areas,” Proceedings of Noise-Con 87, State College, Pennsylvania (June 1987), pp. 233-238.
Gordon, C. G. (1991). “Generic criteria for vibration-sensitive equipment,” Proceedings of SPIE Conference on Vibration Control and Metrology, pp. 71-85, San Jose, CA (November 1991).
Institute of Environmental Sciences (1993), “Considerations in Clean Room Design,” IES-RP-CC012.1
Institute of Environmental Sciences (2005), “Considerations in Clean Room Design,” IES-RP-CC012.2
ISO 14644-4:2001, “Cleanrooms and associated controlled environments—Part 4: Design, construction and start-up,” 51 pp.
Ungar, E. E., and Gordon, C. G. (1983). “Vibration Challenges in Microelectronics Manufacturing,” Shock and Vibration Bulletin, 53(I):51-58 (May 1983).
f3df06a9e162767640cdd8025a54b545Amick, H., and M. Gendreau, “Considerations regarding the appropriate timing for advanced technology facility vibration surveys,” Semiconductor Fabtech, No. 25, March 2005, Cleanroom Section, pp. 1-8.