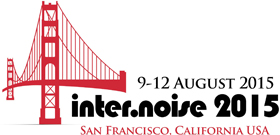
Building expansion and densely developed campuses often require construction adjacent to highly vibration sensitive facilities such as advanced technology manufacturing, laboratories, and hospitals. The vibration generated by the construction work poses a considerable risk to the sensitive processes in these facilities, which typically need to continue operations during construction. In these scenarios it is often advisable to install a vibration monitoring system within the sensitive facility in order to record the construction vibration impacts, report when the vibration criteria are exceeded, and identify problematic vibration sources. The methodology and equipment required to monitor vibration for sensitive facilities differ significantly from more traditional vibration monitoring projects, requiring much more sensitive sensors, more sophisticated data processing, and careful consideration of factors such as sensor placement, equipment sensitivity, alarm thresholds, etc. Specific requirements and considerations for pre-construction measurements, system installation, and continuous monitoring in these facilities are presented via case studies of projects where such systems have been implemented. Potential improvements in procedures and monitoring equipment specifications for future projects are also discussed.
1 INTRODUCTION
As technology advances, the number of facilities utilizing vibration sensitive equipment is continually increasing. Research laboratories, manufacturers of advanced technology devices such as semiconductors and flat panels, and hospitals all utilize processes and equipment that are sensitive to vibration amplitudes well below the threshold of human perception (micro-vibration). Simultaneously, building projects are trending toward compact development in urban areas and densely packed campuses to provide ease of access and to best utilize available space. These trends mean that construction adjacent to existing vibration-sensitive facilities, whether new construction or renovation, is increasingly common. Because most of these sensitive facilities are not able to cease operations while construction takes place nearby, particularly when construction projects can last years, steps and precautions must be taken in order to limit the impact from adjacent construction on the facility. The considerations required for controlling and monitoring the vibration impact from construction on highly vibration-sensitive facilities are quite different from more conventional construction monitoring, which is typically concerned with human perception, environmental noise impact, or preventing building damage.
2 EQUIPMENT VIBRATION SENSITIVITY
There are many types of equipment that are sensitive to micro-vibration. Research facilities may have optical microscopes, electron microscopes, mass spectrometers, and many other instruments that are sensitive to very low levels of vibration. Semiconductor manufacturers use specialized photolithography, metrology, inspection, and other tools that can have very stringent vibration criteria. Hospitals contain MRI and CT Scanners, as well as surgical suites where the use of microscopic surgery and sensitive equipment requires increasingly quieter vibration environments. Excessive vibration impacting these facilities can cause equipment errors that jeopardize experiments, result in loss of valuable product, and, in the case of hospitals, pose a risk to patient health.
The impact that vibration has on an instrument is dependent on not only the amplitude but also the frequency content. An instrument will typically be more sensitive at frequencies around the structural resonances of its internal elements as well as the resonances of any internal or externally incorporated vibration isolation mounts. Therefore, a specific vibration criterion is often developed for each instrument model. In an operating facility, there are usually many types of vibration-sensitive equipment in use with varying vibration criteria. For this reason, generic vibration criteria are often used to cover classes of instruments and equipment. Figure 1 shows the VC criteria for vibration sensitive equipment, developed by Eric Ungar and Colin Gordon in the 1980s1 and further expanded by Amick, Gendreau, and Gordon in 20052, along with the ISO vibration criteria developed for less sensitive spaces. The criteria are presented as one-third octave band rms velocity spectra up to the 80 Hz band. The criteria classes cover general bench top instruments down to highly sensitive imaging systems such as electron microscopes.
The very low amplitudes at which these instruments are sensitive, as well as the varying frequencies at which they are most sensitive, are important considerations when evaluating and monitoring the potential vibration impact from adjacent construction, and the main reason why more traditional approaches (such as those which only consider peak particle velocity) are typically insufficient.
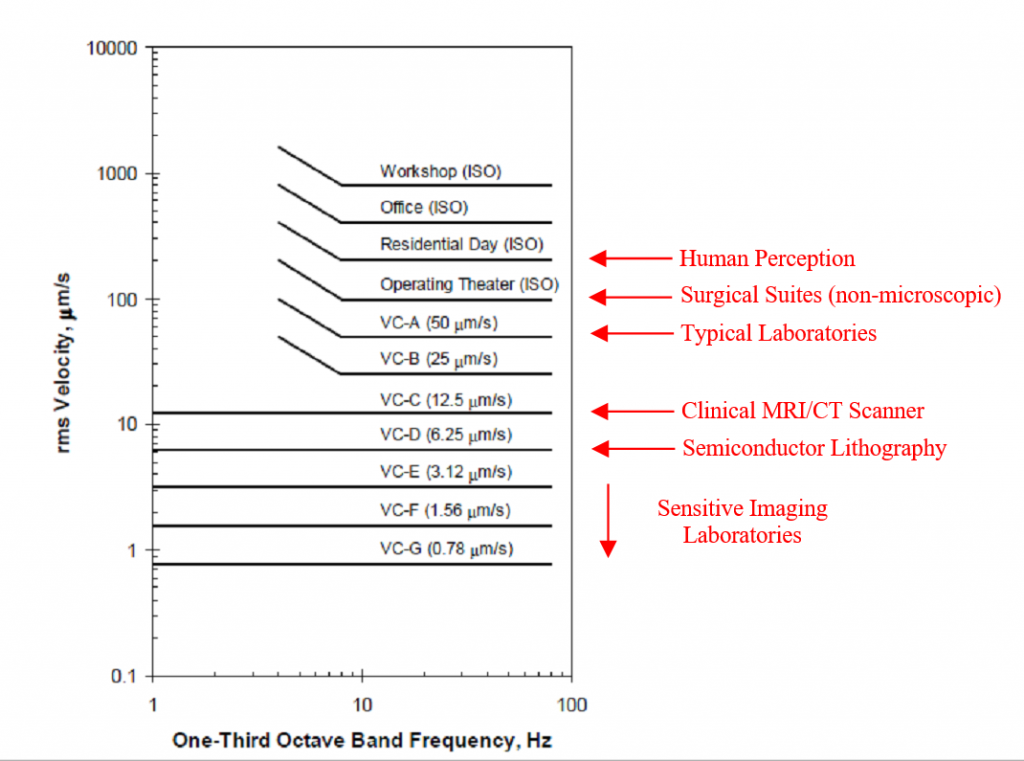
Fig. 1 – Vibration Criteria
3 CONSTRUCTION VIBRATION CONTROL FOR SENSITIVE FACILITIES – TYPICAL APPROACHES
When a sensitive facility is involved, there are a number of ways in which the evaluation and monitoring of construction impact differ from more traditional facilities.
3.1 Pre-Construction Evaluation
The best way to protect a sensitive facility from construction vibration impact is, when possible, to take steps to prevent problematic vibration amplitudes in the first place. Discussion and establishment of appropriate vibration criteria should take place well before the beginning of construction. Unlike environmental noise, or vibration monitoring for building damage, or human comfort, there are no established universal criteria for vibration impact on sensitive facilities; although potential strategies for establishing regulations have been proposed3. Establishment of criteria requires an evaluation of the tool sensitivity within the existing facility, as well as the current vibration environment in the facility prior to construction. Having defined criteria will allow the invested parties to plan out vibration control methods and protocols for protecting the sensitive facility from construction vibrations.
General guidelines regarding construction vibration control for the project can be provided based on those developed from prior projects and experiences. These guidelines typically contain recommended safe setback distances for various construction activities and equipment, as well as recommended techniques for vibration control. However, general guidelines are only recommended for use as a starting point in establishing a vibration control plan. As soil and structural dynamics can vary from site to site, general guidelines may not provide accurate setback distance recommendations for the particular site in question. For this reason, we typically recommend that pre-construction vibration testing with staged controlled construction activities be conducted prior to the beginning of construction4. The objective of the staged testing is to evaluate the vibration transfer characteristics of the site, which would allow the general guidelines recommendations to be refined and calibrated for the specific site conditions. The staged testing would also allow for evaluating activities for which guidelines have not yet been developed, or for evaluating specific activities which are particularly concerning.
3.2 Vibration Monitoring System
Once vibration criteria have been established and a construction vibration control plan has been put in place, a monitoring system can be installed. The monitoring system should have the ability to continuously analyze the vibration amplitudes in the sensitive facility and compare these to the established criteria. When an exceedance is detected, a number of actions can take place, such as recording/documenting the event, and sending an alert to the construction team.
A vibration monitoring system typically consists of one or more sensors, normally accelerometers, attached to a data collection device, which provides power to the sensors and converts the analog signal to a digital format. The vibration data collected is recorded, manipulated, and analyzed using a data processing unit that is either integral to the data collection device or a separate unit, such as a laptop computer. The system continuously gathers data from each sensor, compares the measured data to an adjustable threshold, and performs certain actions and sends notifications if that threshold is exceeded. An internet or network connection to the data processing device is typically required in order to send exceedance notices via email or text, as well as to allow for the system to be viewed and manipulated remotely.
A number of vibration monitoring systems are available off-the-shelf, though these have been primarily developed with human comfort and building damage in mind. While these systems do have the ability to continuously analyze vibration amplitudes and send out alerts in case of exceedances, these systems are not sufficient for monitoring for vibration sensitive facilities, for two major reasons:
- Traditional vibration monitoring systems are not designed to measure extremely low amplitudes (i.e. micro-vibrations) that can impact vibration-sensitive equipment. The accelerometers associated with traditional systems typically have low sensitivity and high noise floor, meaning that low level vibrations will be masked by system noise.
- Most off-the-shelf monitoring systems simply measure the overall amplitude, and are not able to report or compare to thresholds in the frequency domain. As discussed above, most vibration-sensitive equipment have criteria defined as a function of frequency, therefore an overall level is insufficient.
A monitoring system installed in a vibration-sensitive facility should have the following characteristics:
- The system should use highly sensitive accelerometers to accurately measure low vibration amplitudes, on the order of 10 V/ g.
- The system should be capable of measuring and comparing to thresholds in the frequency domain. Thresholds should be adjustable by individual frequency band, with a minimum resolution of one-third octave bands.
- The averaging time should be adjustable, to account for the varying duration over which a vibration-sensitive tool or process may be sensitive5.
- The system should be multi-channel in order to record and analyze multiple locations synchronously. This will allow for quick and direct comparisons between locations, source localization, as well as setting of correlated thresholds between channels if necessary.
- The system should be capable of recording time history data for post-processing purposes. This capability is key for analysis of threshold exceedances after the fact in order to characterize and identify the source of any problematic vibration. Post-analysis may be required to determine the specific source, particularly on large construction projects or large facilities where the source may not be obvious from the time, location, and captured spectra alone.
- The system should be able to trigger visual, audible, and/or electronic alerts, depending on the users’ preference, upon the exceedance of a threshold. Electronic alerts can be in the form of text message, email, or an update to a web-based log. This requires that at a data connection be provided for the unit.
- The system should also be set up to allow remote access. As the system will be located on-site and primarily unattended, remote access would allow operators offsite to troubleshoot, download and process data, revise thresholds, etc. This may require different permission setups for different users.
Some of the above requirements will depend on the specific needs or requests from the building users or contractors. However most of the features listed above are required on any system to be used to monitor vibration within a sensitive facility.
4 EXAMPLE SYSTEMS
The following section contains examples of projects where construction adjacent to a vibration-sensitive facility took place, and the procedures and systems used to prevent and monitor construction vibration impact.
4.1 System 1 – New Building Construction Adjacent to Research Facility
In this project a number of new facilities are being constructed on multiple sides of an existing basement physics lab on a University campus in California. This basement lab contains highly sensitive equipment, with a vibration criterion of VC-E. As the planned facilities and associated construction is to come within just a few meters of the existing lab, vibration impact from this construction is a significant concern.
Our project input began with meetings with the lab users to understand the nature and sensitivity of their work, as well as their concerns regarding impact to their lab. We also met with the University facilities personnel who would oversee the construction projects to discuss the planned construction activities and provided recommendations for how best to limit the impact to the existing lab. A vibration monitoring system was installed within the lab to address the concerns of the researchers about impact to their work, as well as provide accountability for the construction contractors.
The vibration monitoring system used for this project involved three accelerometers measuring triaxial vibration at one location within the sensitive lab. The accelerometers were connected to a data analyzer that was operated by a laptop computer running a customized macro that controlled the data acquisition parameters. The monitoring system was installed well before the beginning of construction in order to document the background ambient levels, as well as any vibration impacts that may be generated by sources other than construction. These pre-construction measurements are particularly crucial when monitoring at very low levels, as there are any number of sources other than construction that may generate low amplitude vibration that may or may not be of concern to the facility. Identifying these sources prior to construction helps to prevent vibration issues from being incorrectly associated with construction.
No alarms or other triggered events were required in this case as the goal was primarily to document the vibration amplitudes in the lab over the course of construction. The system was set up to continuously log 60-second averages of one-third octave vibration amplitudes, as well as continually record the vibration time history. A 60 second average was chosen as a suitable duration to provide a summary of the variation in vibration amplitudes without an overwhelming amount of data. Evaluation of vibration impact over shorter durations could be conducted using the saved time history data.
Each week a summary of the vibration amplitudes logged over the previous week was provided to the users. These reports included contour plots of the vibration amplitudes versus time, as a function of frequency, as shown in Figure 2. The first plot in this figure is an example of a contour plot showing a vibration impact that was likely related to construction. The second plot shows continuous vibration that was measured before and during construction, indicating that this vibration is due to a source other than construction, such as building mechanical system. Events that looked construction related were identified and documented in the weekly reports. One can usually see when construction work started in the morning and ended in the afternoon as the number of impact events corresponded accordingly.
Construction Impact:
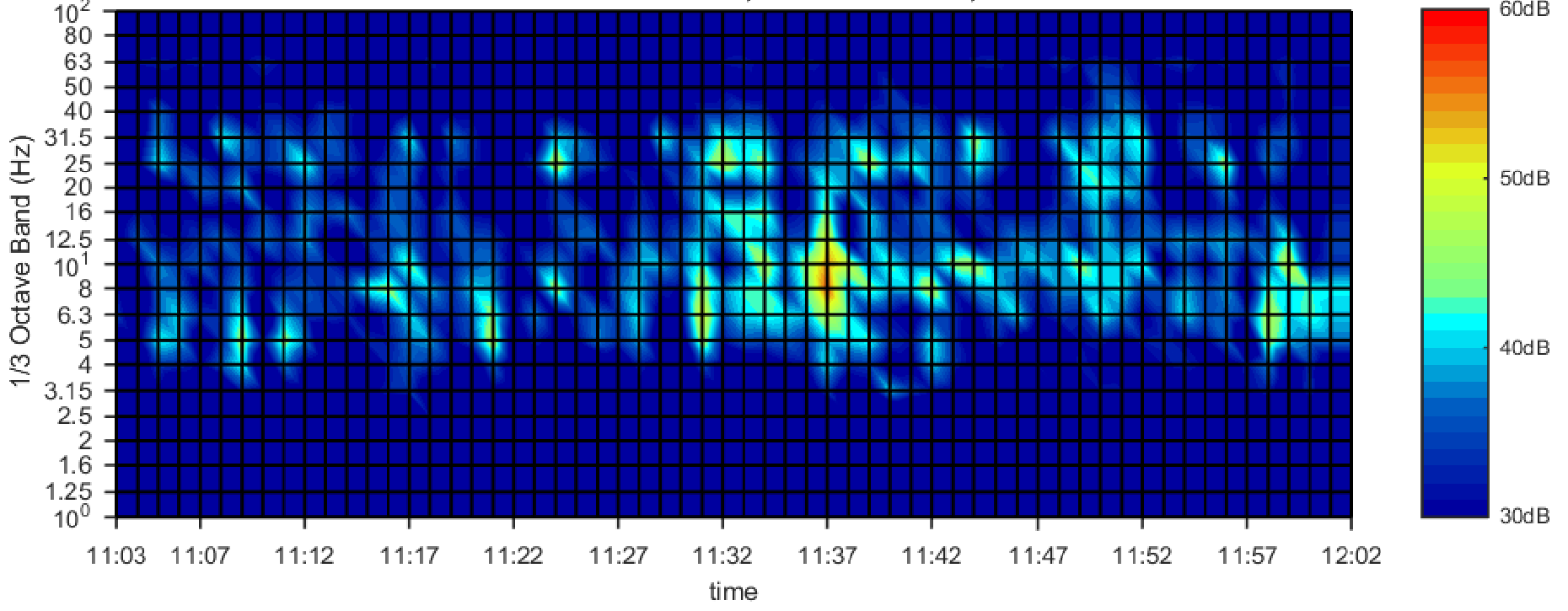
Building Mechanical Source Unrelated to Construction:
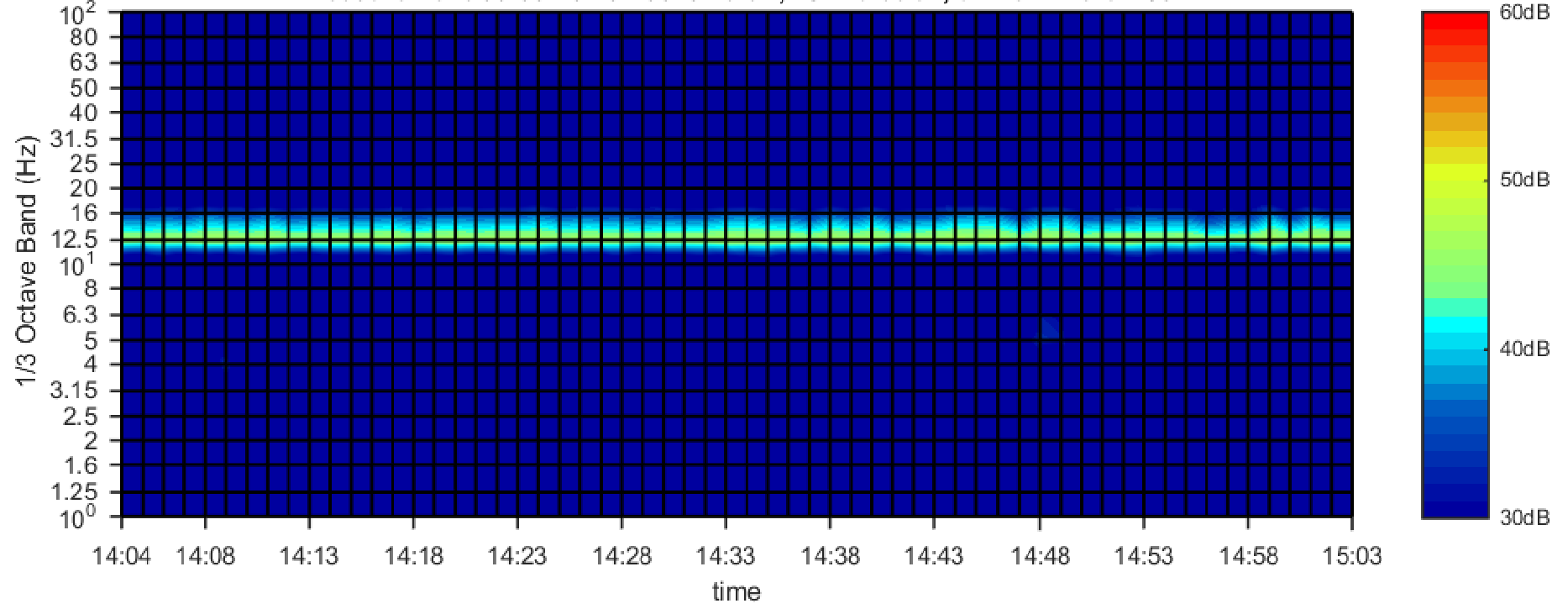
Fig. 2 – Example Hourly Surface Plots.
The continuously logged spectra also allows for the vibration levels over the course of a typical day, week, or month during construction to be summarized statistically, as shown in Figure 3. These statistical summaries provide the users and facilities personnel a quick high-level overview of the vibration impact from construction over a given time period, in the form of various centiles6 commonly used in environmental noise. In this case, the VC-E criterion was exceeded approximately 5-percent of the time during the period of interest.
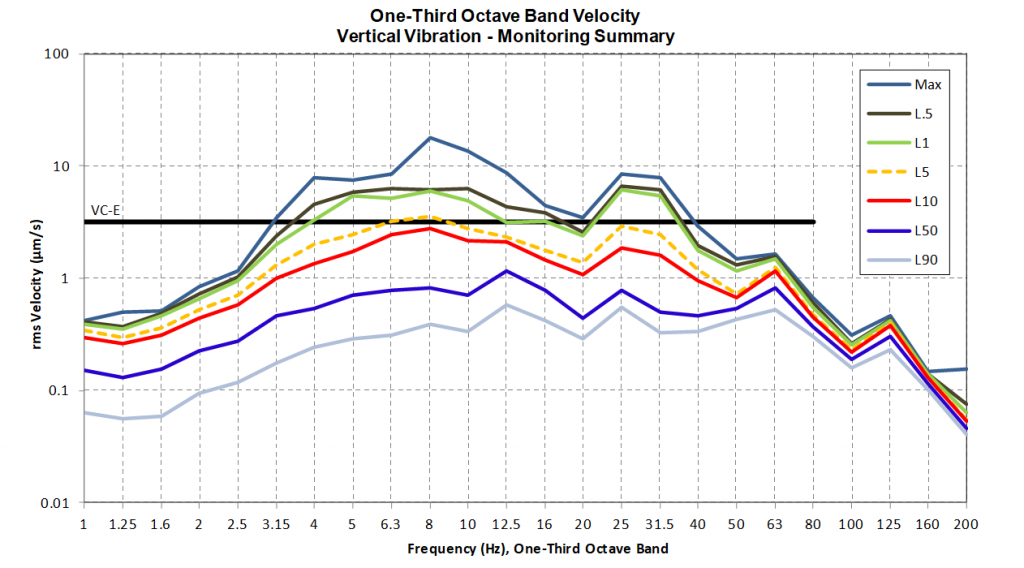
Fig. 3 – Example Monitoring Summary Plot
4.2 System 2 – New Semiconductor Production Facility
A semiconductor manufacturer was planning to construct a new production facility directly adjacent to, and physically connected to, an existing active manufacturing building. The sensitive tools in the existing facility were predominantly located on the third level, on a concrete waffle floor, with some photolithography equipment having a criterion as stringent as VC-D. Vibration impact from this new construction was of great concern, as the existing facility operated 24/7, and any vibration impact could result in serious disruption of production, lost product, and a great deal of revenue loss.
As with the previous project, control of the construction vibration impact from the new facility began with input and recommendations on the construction process. Vibration and forcing function data from earth moving equipment, large truck traffic, compactors, and cranes measured during a previous study at the site was used to establish minimum recommended setback distances from the sensitive building for associated construction activities. These setback distances along with general guidelines were included as part of the construction document requirements provided to the contractor.
In addition to these construction vibration control measures, a vibration monitoring system was installed in the existing facility. Since the area of concern was very large, with over 90,000 m2 of vibration sensitive process floor, with a complicated structure, this required a more sophisticated system than System 1 described above. An array of 16 sensors were installed throughout the facility, with sensors oriented in the vertical direction as well as the horizontal direction toward the construction site, all of which were wired to a central analyzer and operated by a laptop computer.
Sensors were placed in typical structural bays such that all worst-case sensitive locations with regard to proximity to construction were represented, and were installed at varying setback distances away from the construction site in order to allow for triangulation of sources based on the relative amplitude of the measured vibration. The majority of the sensors were attached directly to the bottom side of the third level concrete waffle floor, which was the most critical sensitive floor.
The system display, which could be viewed and manipulated remotely via an internet connection, showed the real-time vibration amplitudes at each location versus the alarm threshold, as shown in Figure 4. A custom macro was programmed to continuously monitor the vibration levels and send out an alert via email to the facility users when vibration exceeded a given threshold.
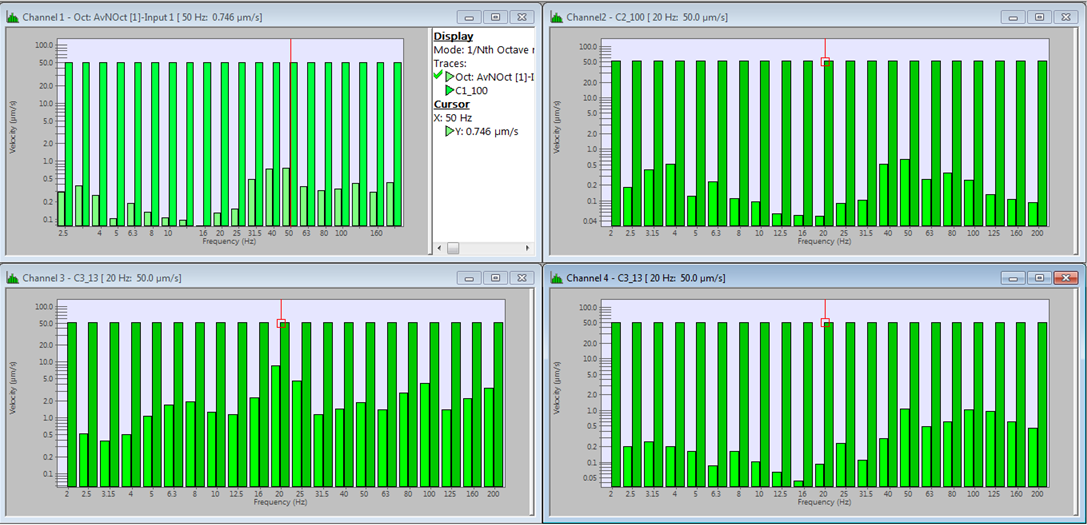
Fig. 4 – Example Display: Current Levels vs. Thresholds
To further ensure that any threshold exceedance was due to construction and not some local activity (e.g. repair work on a nearby tool), threshold exceedances on the suspended floor were set to only trigger an alarm if a corresponding threshold was exceeded on the slab-on-grade directly below. This helped to ensure that the problematic vibration was due to construction, as a construction vibration would necessarily travel through the slab-on-grade before reaching the sensitive suspended floor. This is illustrated in Figure 5.
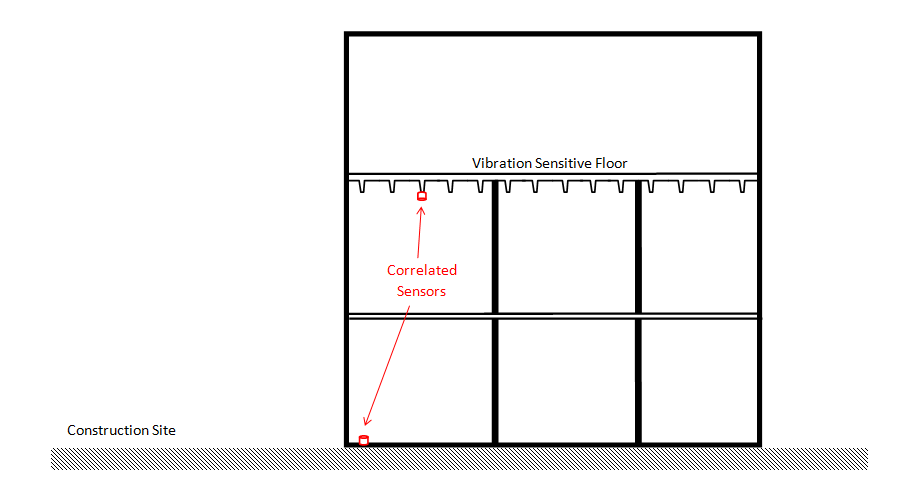
Fig. 5 – Correlated Sensors
If the measured amplitudes on the sensitive floor exceeded the threshold, and correlated with elevated amplitudes on the ground below, the system would then capture and save the one-third octave band spectra on all channels, record the time history data for 30 seconds before and 60 seconds after the threshold was exceeded, and send an alert email out to the users with a report containing the time and location of the exceedance, as well as the captured spectra on each channel in comparison with the alarm thresholds. An example of the spectra contained in a typical report is shown in Figure 6. The frequency content and relative amplitudes of the spectra at each location could often be used to help identify the source of the problematic vibration.
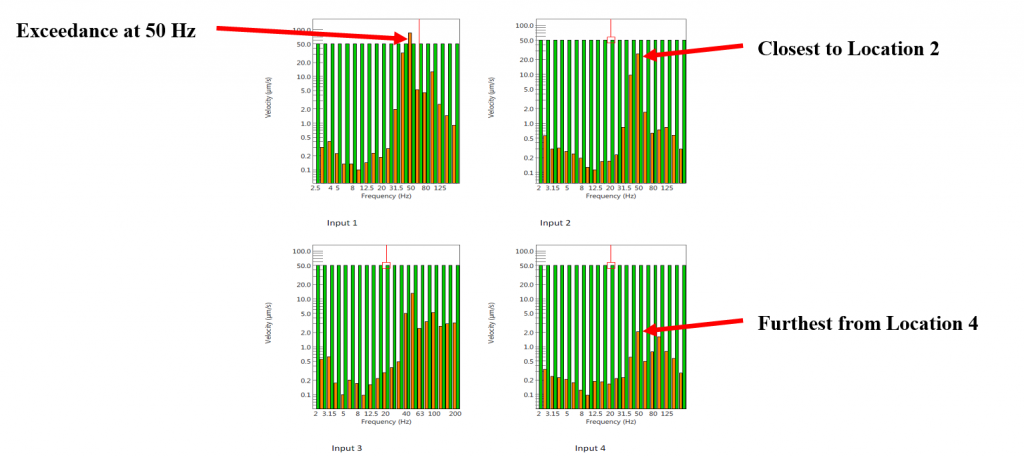
Fig. 6 – Example Reported Spectra
4.3 System 3 –Semiconductor Production Facility Renovation
System 3 involved another semiconductor production facility that was being renovated in order to make way for a new facility. The renovation involved the removal of a large section of the building, which required the demolition of the concrete floor slab, walls, and roof structure. All of this work was to take place directly adjacent to a continuously operating vibration-sensitive production floor (on-grade).
As in the previous cases, the process began with input into the construction means and methods with regard to vibration control. In this case staged construction vibration measurements of the exact proposed construction activities were conducted, including saw cutting the floor slab, compacting, drilling, etc. at a location within the facility, but far from sensitive equipment. One of the goals of the staged measurements was to determine which concrete removal technique was the least intrusive. Another goal was to determine how the vibration attenuates with distance across the sensitive facility so that a safe setback zone could be established for each type of activity. This measurement data was used to provide construction vibration control guidelines to the contractor.
Prior to the beginning of construction, a vibration monitoring system was installed inside the sensitive facility. Seven vibration sensors were installed along the perimeter of the facility on the slab-on-grade, nearest to the proposed renovation work. A system similar to System 2 was installed to continuously monitor the vibration levels and record and send alerts on threshold exceedances, although in this case correlation between sensors was not necessary. In addition to email alerts, this system would also activate two flashing beacons when a threshold was exceeded. One beacon was located inside the production facility, while the other was mounted on the outside of the building where it could be seen by the construction team. This immediate visual feedback provided a much more direct connection between the facility and contractor, and allowed any problematic construction activities to be ceased immediately. The system was set such that the beacon would continue to flash, even as the system returned to monitoring, until someone within the facility turned it off. This ensured that someone was aware that a threshold had been exceeded.
An additional update to this system involved the averaging time. One of the issues with vibration monitoring for sensitive facilities is that false alarms are common. Events that may occur often, such as a dropped hand tool, kicked raised floor tile, or inadvertent disturbances of sensors and cabling, would typically have no impact on the sensitive tools in question. These short impacts are not of sufficient duration to overcome the large mass and internal damping within the tools. For System 3, false alarms were reduced by requiring that a threshold be exceeded for two consecutive averages, which ensured that the vibration exceeding the threshold was of sufficient duration to be a concern.
When thresholds were exceeded, construction activities were immediately ceased until the source of the vibration could be identified and remedied. The sensitive tools nearest the sensor(s) that exceeded the thresholds were then checked for errors. As the monitoring system was located on the process floor, in close proximity to the construction site, vibration impact from construction activities could also be monitored in real-time and feedback provided to the contractor.
In some cases, further analysis of the measured data was required in order to determine the source of the problematic vibration. Figure 7 shows the captured spectra from one such case. The spectra showed that the problematic vibration had its greatest impact in the 40 Hz one-third octave band, and based on the relative amplitudes in this frequency band, the source was likely closest to Locations 1 and 3. An FFT analysis of the recorded time history data showed that the problematic vibration was due to a tone at 38.4 Hz, as shown in Figure 8. A tone is vibration occurring at one specific frequency, typically associated with rotating equipment. In this case the tone at 38.4 Hz corresponds with equipment rotating at 2304 revolutions-per-minute (rpm). This information, combined with the location and duration of the measured vibration, led to the source of the problematic vibration to be identified as a compressor used periodically by the construction crew. Similar frequency analysis enabled other unknown sources to be identified as well, such as high frequency tonal impact from saw cutting, low frequency broadband impact from dropped loads, etc. Network access to the system allowed for all of this support and analysis to be provided remotely, and for issues to be resolved quickly, saving valuable construction and production time.
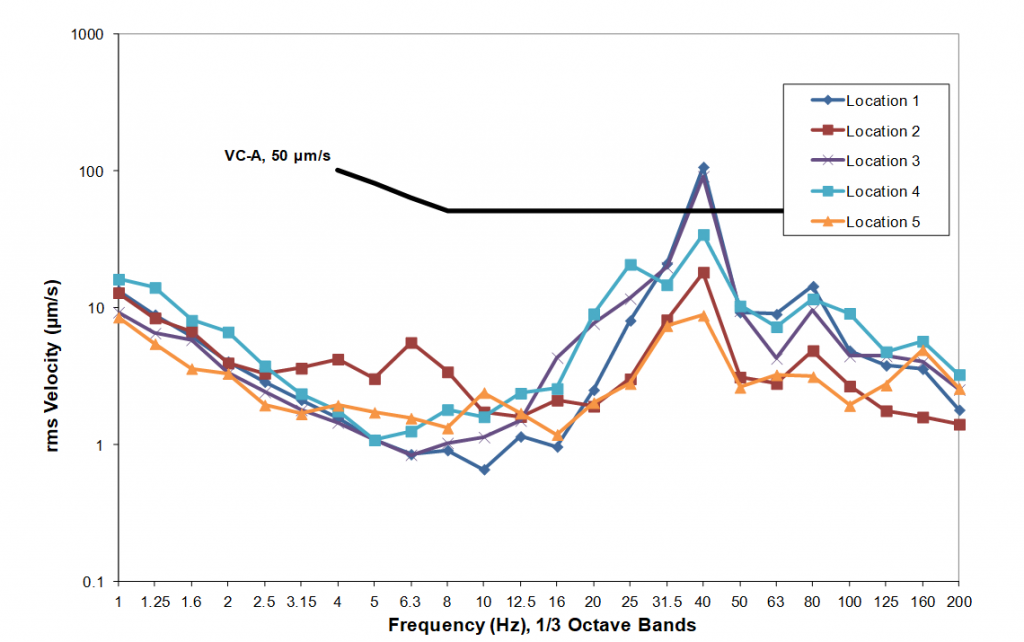
Fig. 7 – Threshold Exceedance in 40 Hz Band
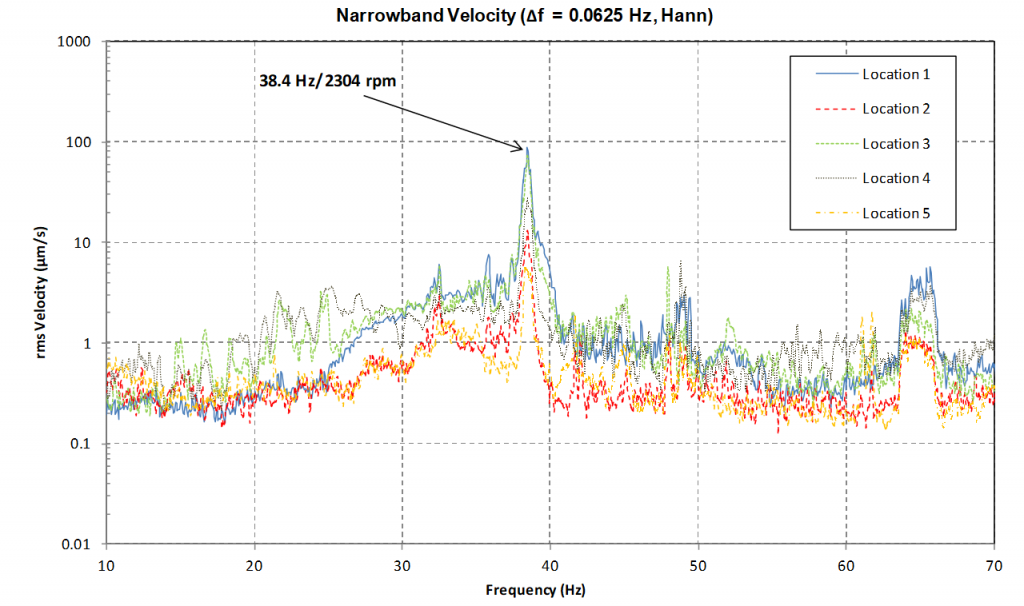
Fig. 8 – Analysis of unknown vibration source
5 CONCLUSIONS
Increasing vibration sensitivity of facilities and density of development, as well as more aggressive construction timetables, mean that construction vibration impact on sensitive facilities will continue to be a growing concern. The capabilities of monitoring systems used to protect such facilities from construction vibration impact will need to continue to improve. The systems outlined here provide a basis for what is required for highly sensitive facilities, however future systems must expand on the features and capabilities described here to meet the expanding needs and demands of facilities where maintaining a quiet vibration environment is paramount to their existence. Future systems must be designed to be highly customizable to meet the needs of each facility and project. Increased automation of actions and reporting is necessary to handle more complicated tasks at lower cost. Improvements in wireless technology and portability would allow such systems to be installed more quickly and easily, and provide increased flexibility in the location and layout of the systems. Finally, improved user interfaces would allow for more involvement from and better communication between the facility users and construction.
Vibration monitoring systems are an effective tool for limiting the potential impact of construction activities on vibration-sensitive facilities. However, such systems can only be used to notify of an exceedance after the fact. As outlined above, successfully protecting a vibration-sensitive facility from construction activities requires a significant amount of coordination between the contractor, users of the sensitive facility, and vibration consultant prior to and throughout the construction process.
6 ACKNOWLEDGEMENTS
Assistance in the development of many of the systems used in the above studies was provided by John Woods of OROS, Inc, and we would like to thank him for his efforts.
7 REFERENCES
- C. Gordon “Generic Criteria for Vibration-Sensitive Equipment”, Vibration Control in Microelectronics, Optics, and Metrology, SPIE Proceedings Volume 1619, pp. 71-85, San Jose, CA (Nov. 1991)
- H. Amick, M. Gendreau, T. Busch, and C. Gordon, “Evolving Criteria for Research Facilities: Vibration,” Proceedings of SPIE Conference 5933: Buildings for Nanoscale Research and Beyond, San Diego, CA (Jul. 2005)
- R. E. Nugent and H. Amick, “Vibration Considerations in Zoning,” Proceedings of Inter-Noise 89, Newport Beach, CA (Dec 1989)
- See H. Amick and M. Gendreau, “Construction Vibrations and Their Impact on Vibration-Sensitive Facilities,” Proceedings of the Sixth Construction Congress, ASCE, pp. 758-767, Orlando, FL (Feb 2000) for a detailed discussion of the approach to site-specific assessment of the impact of construction vibrations on vibration-sensitive facilities.
- H. Amick, “On Generic Vibration Criteria for Advanced Technology Facilities: with a Tutorial on Vibration Data Representation,” J. Institute of Environmental Sciences, pp. 35-44, (Sept/Oct 1997) contains a discussion of time averaging considerations required for vibration-sensitive equipment and processes.
- Centile metrics express the percentage of time that a given amplitude is exceeded. L50 represents the vibration level exceeded 50% of the time, L1 the level exceeded 1% of the time, etc. See H. Amick, M. Gendreau, and N. Wongprasert, “Centile Spectra, Measurement Times, and Statistics of Ground Vibration,” in Environmental Vibrations: Prediction, Monitoring, and Evaluation, ISEV2005, ed. H. Takemiya, Taylor & Francis, (2005)
a) email: steven.lank@colingordon.comb) email: blong.xiong@colingordon.com ↑